Statistical model development to anticipate filter breakthrough and optimise chemicals during high colour raw water events
By A Mohiuddin and Y Wang.
First published in Water e-Journal Vol 2 No 4 2017.
Abstract
Sydney Water operates the Nepean Water Filtration Plant (WFP) which has been receiving raw water with higher true colour from the Nepean dam in recent years. It was evident from higher true colour raw water that lower floc strength is the key issue, which causes filter breakthrough, resulting in significant decrease in filters run time, hence reduction of a plant’s production rate. Therefore, a statistical process model was developed to anticipate filter breakthrough during higher colour of raw water and to optimise chemicals to prevent filter breakthrough. The process model analysed the previous four years’ performance data of all dual media gravity filters, and developed correlation of filter breakthrough/performance with raw water qualities, chemicals dose rates, filter design and filter performance indicators.
As an output, the process model can predict any filter turbidity breakthrough and plant performance deterioration, can provide instantaneous optimised chemical dose rates to stop filter breakthrough, and can save chemical usage and operator response time, providing a continuous optimisation guide to plant operators. The developed process model was applied at Nepean WFP during October to December 2016 in high colour event for raw water true colour at 25 HU @400 nm. This successfully eliminated the filters’ turbidity breakthrough, increased plant production rate by 31%, increased all the filters run time by 60-300% and achieved significant chemical savings in the range of 20- 51%. The developed process model can be applied to any water filtration plant for process optimisation.
Introduction
Sydney Water operates the Nepean WFP, which treats raw water from the Nepean Dam, south-west of Sydney. The process train at Nepean WFP consists of raw water pre-treatment by chlorine, lime, potassium permanganate (KMnO4) and carbon dioxide (CO2) dosing followed by coagulation-flocculation using ferric chloride, cationic polymer (poly-DADMAC) and nonionic polymer (Polyacrylamides) dosing; then first stage clarification by roughing filters (micro-floc adsorption clarifier); and final stage filtration by dual media gravity filters. Historically, this plant has been operating at 230-240 L/s, running one of the three fixed-speed raw water pumps under normal raw water turbidity 1-5 NTU and true colour 10-18 HU (@400 nm). In 2012, following a wet weather event, raw water true colour increased, quickly reached to 40-45 HU, then gradually decreased over the next 12 months.
Since then, every year raw water true colour reaches to a peak of above 30 HU and then gradually decreases over a period but never reverts to the historical average true colour (Figure 1). Colour reflects various compounds in the raw water, mainly the organic fractions, and hence is used as a surrogate parameter to exhibit presence of organic matter in water. The higher true colour in the raw water over the past number of years has also been complicated by historically lower turbidity over the same period. This higher colour and lower turbidity source water has presented considerable challenges to Sydney Water in maintaining filter performance (Mohiuddin et al. 2014).
It was evident from higher colour raw water that lower floc strength is the key issue, which causes turbidity breakthrough in dual media gravity filters (Figure 2). Consequently, the plant’s production rate was reduced to 150-160 L/s (34% reduction) (Figure 3) and the dual media filters’ run time was significantly reduced to 10-15 hours (69% reduction). Chemical optimisation at the plant, carried out in the last few years, improved filter performance and the plant’s production rate. However, because of the unpredictability of filter breakthrough and longer time required in optimisation to improve floc strength, the plant’s production rate and the filters’ performance were immediately reduced at the start of each raw water high colour event. Therefore, a statistical process model was developed by the authors to anticipate filter breakthrough during higher true colour of raw water and to instantly optimise chemicals to prevent filter breakthrough, maintain the filters’ performance and plant production rate.
Development of the process model
The statistical process model used the previous four years’ performance data of the dual media gravity filters, and analysed the parameters during each filter turbidity breakthrough. The analysis included filter performance statistics, filter backwash triggers, coagulation conditions, every chemical dose in treatment, filter design parameters, filter media specifications and raw water qualities.
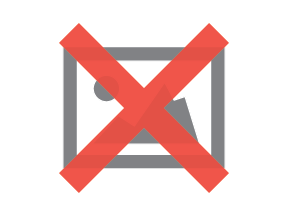
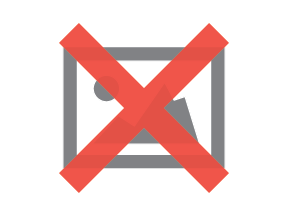
The process model then correlated all these parameters and differentiated between the optimum and suboptimal condition of the plant under a range of model input scenarios. Figure 4 shows the inputs to the model covering:
- Raw water qualities
- Filters’ performance data
- Chemical dosing – including pre-treatment, coagulation and post-treatment
- Other parameters of the plant (roughing filter performance, hydraulic loading, filter design, filter media specification, etc.)
From these inputs, the model developed the following equation to anticipate filter breakthrough:
Filter breakthrough = f (raw water quality, chemical dose rates, filter design, filter performance indicators)
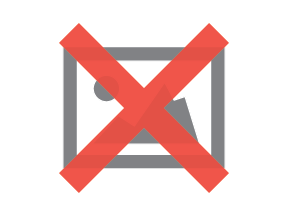
Output and results of the statistical process model
As an output:
- The statistical process model can predict filter turbidity breakthrough and plant performance deterioration during any sudden rise of raw water true colour (model calculated plant’s performance at current raw water quality and chemical dose rates).
- The statistical process model can provide instantaneous optimum chemical dosages to eliminate the filter breakthrough due to changes in raw water quality and anticipate the plant’s performance at model optimum chemical doses (optimisation using the model and forecast of plant performance improvement).
- For process data analysis, the model user can select a wide range of data sets from data selection criteria to see all the correlations among the parameters.
The model user can easily compare model-calculated filter performance at the current plant parameters and model-predicted performance with model-suggested optimised parameters. Plant operators can then choose to optimise chemicals, based on the model-calculated optimised parameters. Outcomes of the model focus on improved water quality, reduced filter breakthrough, increased plant production and filters’ run time, chemical savings, and savings in operator response time to optimise chemicals during raw water quality changes.
Application of the developed process model
The developed process model was applied at Nepean WFP during October to December 2016. In October 2016, raw water turbidity and true colour was 1-2 NTU and 25-26 HU respectively. All the dual media gravidity filters were experiencing severe turbidity breakthrough (Figure 5 and 6) and as a consequence filters’ run time was decreased to the range of 10-25 hours (Table 1). The plant production rate was reduced to 180 L/s (Figure 6, Table 1) which limited the plant net production capacity to around 14 ML/d excluding the filter backwash water.
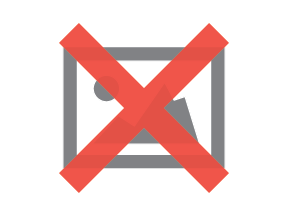
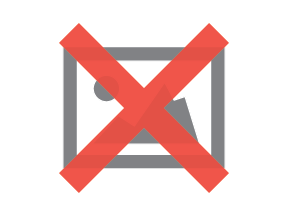
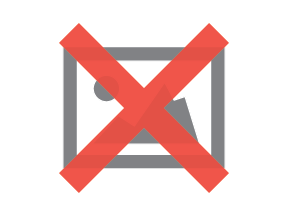
Due to lower production from the plant and higher water demand in the network, the main reservoir (13.5 ML capacity) level was occasionally dropping to critical level. This indicated severe depletion of network water storage and sometimes it took a few days to catch up the depletion when water demand became lower than the plant’s production.
The developed process model was applied at that time in October 2016. The process model indicated severe breakthrough in all dual media gravity filters and demonstrated that the filters’ breakthrough could be corrected by optimising the chemicals.
The model predicted optimum chemical dosages at that condition showed far different dose rates than the existing dose rates at the plant (Table 1). By implementing the process model, the chemical dose rates were gradually adjusted over the period of November to December 2016. This has fully eliminated the filters’ turbidity breakthroughs at that condition (Figure 7), increased the plant production rate by 31% (235 L/s) (Figure 7, Table 1), increased all the filters’ run times by 60-300% (40-48 hours) and achieved significant chemical savings in the range of 20-51% (Table 1).
Conclusion
The statistical process model is a very quick guide for the plant operators to anticipate potential plant performance issues relating to raw water quality change. The process model correlates parameters and can use the live data from SCADA and provides instantaneously calculated information of filter breakthrough and suggested optimum chemical dosages. The model can continuously suggest to the plant operators the optimum chemical dosages for any raw water condition, saving operators’ response times during a plant emergency, preventing plant performance deterioration and saving costs from un-optimised chemical dosages. The developed process model is fully transferrable and can be applied to any water filtration plant for process optimisation.
Acknowledgement
Thank you to the Nepean WFP team for their cooperation and active contribution to optimise the plant using process model suggested optimum dose rates of chemicals. The authors would also like to acknowledge the cooperation of their colleagues in Sydney Water for their support in the development of this process model.
About the authors
Asm Mohiuddin | Asm is a Process and Technology Manager in Customer Delivery – Treatment in Sydney Water. He is currently working on Drinking Water and Recycled Water Improvement projects and leading an innovation and process optimisation team. He has 15 years of process engineering experience in petroleum, water and wastewater industries. He has a Bachelor of Science degree in Chemical Engineering and Master of Engineering degree in Water, Wastewater and Waste Engineering.
Yue-cong Wang | Yue-cong is a Modelling Specialist at Sydney Water. He has over 28 years of numerical modelling and model development experience gained through practical and research activities in water and wastewater fields. He also has very strong computer programming skills and has developed many customised softwares for data manipulation, management and presentation in support of hydraulic and environmental modelling activities as well as water quality monitoring.