Energy management at Allwater
By J Dreyfus, G Oates.
First published in Water e-Journal Vol 4 No 4 2019.
Abstract
Allwater operates and maintains Adelaide’s water and wastewater systems and has an electricity consumption of approximately 93,000 MWh per annum. In 2013, Allwater developed an ISO 50001 certified Energy Management Program to better meet its sustainability responsibilities. Key steps involved understanding existing energy consumption, deployment of staff awareness initiatives and development of a system for ongoing staff input into energy improvements. Subsequent implementation of a number of initiatives has reduced Allwater’s imported electricity by 20%. Allwater has maintained ISO 50001 certification and is committed to continual improvement to assist our Alliance partner, SA Water, achieve their objective of zero net electricity cost by 2020.
Introduction
Allwater (a joint venture between Broadspectrum and SUEZ) operates and maintains the Adelaide Metropolitan Water and Wastewater Supply Systems through the Adelaide Services Alliance. Allwater serves approximately 1.3 million people, with energy usage of approximately 93,000 MWh and greenhouse gas emissions of approximately 69,000 tonnes of CO2 in 2017/18.
The majority of Allwater’s energy consumption is from key processes including (Figure 1):
- Treating raw source water to a drinking water standard;
- Pumping drinking water through the distribution supply network;
- Pumping wastewater (where required) through the sewer network;
- Treating wastewater to a standard appropriate for discharge to receiving waters or for reuse.
In 2013 Allwater commenced the journey to develop an ISO 50001 certified Energy Management Program to better meet its sustainability responsibilities through reducing electricity consumption, maximising power generation (electricity from biogas), and in turn reducing greenhouse gas emissions. In addition, energy management was identified as a key area that can demonstrate both business and operational efficiency to the customer.
The first step in developing the Energy Management Program was to understand the power usage across the business to identify opportunities for improvement. Training and awareness initiatives were developed and delivered which empowered personnel to manage energy effectively. Accompanying this was the development of a process for all staff within Allwater to submit energy efficiency ideas leading to many innovative solutions across all areas of the business.
Since the commencement of the program, large savings in energy have been achieved without compromising service to the customer. The process is ongoing and further work is being undertaken to provide smarter tools to dynamically manage our electricity usage and energy production in the context of electricity being purchased on the spot market by our Alliance partner, SA Water.
This paper outlines Allwater’s energy management journey over the past five years and the lessons learnt, together with details of some of the innovative ideas implemented throughout the business which have led to significant energy savings and recovery.
A journey towards ISO 50001
Allwater made a strategic decision in May 2013 to develop an Energy Management Plan and adopt the ISO 50001:2011 Energy Management System (EnMS) framework to assist the planning process and to ensure ongoing improvement. Figure 2 outlines the steps in the framework.
An energy review was undertaken to capture and define the significant areas of energy usage within Allwater’s operations. As part of this process, energy data from water and wastewater treatment plants together with major pumping stations was analysed. This analysis was used to identify parameters to enable Energy Performance Indicators (EnPIs) and baselines to be established. EnPIs are quantitative relationships between energy consumption and one or more relevant variables, such as the number of filters online to produce drinking water, or the number of pump run hours. Examples of the energy performance indicators are summarised in Table 1. This allowed Allwater to understand and rank energy efficiency performance, highlighting operational areas to focus resources and implement efficiency programs.
Individual baselines were developed for the individual wastewater, water treatment plants and pump stations so that potential energy savings could be highlighted and to initiate investigations into improving efficiency. This also allows the verification and direct measurement of energy savings to be calculated to show continuous improvement and compliance with the ISO 50001 accreditation.
In summary, a total of approximately 120 days were spent incorporating the Energy Management Program into Allwater’s operations. The energy review and data collection were the areas that needed the greatest effort; followed by developing procedures and documentation. The procedures and documentation were then incorporated into daily operations through a communication plan, training and awareness.
After five years of maintaining the Energy Management Plan the energy review is still the largest and most important component of required time and resources to maintain the certification. However, the emphasis has shifted from developing the indicators and establishing baselines, to providing current and easily accessible energy performance information to Allwater personnel on a weekly and monthly basis.
Energy performance targets were set to drive improvements across Allwater. At the end of each financial year the energy performance for each site is reviewed relative to its baseline. In addition, every two years a new review is undertaken to identify the significant energy users for Allwater and also the main sources of power generation to assist with identifying further energy improvement opportunities. Allwater is now entering the third cycle of Energy Reviews, with the initial Energy Review undertaken in July 2014. Each review incorporates a baseline period of the previous 24 months of data to incorporate varying seasonal effects.
ISO 50001 Energy Management System certification was achieved in August 2014. Of significant note is that Allwater took the innovative step to become the first water utility within Australia (and to our knowledge within the Southern Hemisphere) to have their Energy Management Program certified against the ISO 50001 standard.
Maintaining ISO 50001
Internal and external audits of the Energy Management Program have been undertaken in line with ISO 9001 and ISO 50001 requirements. All audits include a walk around the worksite to observe and make suggestions about possible energy savings. The audit program helps to maintain focus and enthusiasm for energy efficiency across the business.
The main focus to maintain ISO 50001 is to achieve the targets every 2 years set during the re-accreditation audits to reduce the whole company energy consumption. Initially the first review targeted 3%; the 2016 review a further 6% by July 2018; and the most recent one is targetting 1% by July 2020. Those targets are set depending on the potential savings, initiatives, and capital development that the business and the auditor have identified.
To ensure that all initiatives are captured all staff within Allwater have had an an awareness training on ISO 50001 and are able to submit energy efficiency ideas through our Better Way program. These projects ensure active involvement in energy saving ideas allowing energy efficient practices to be integrated into daily operations. This has led to a number of personnel-initiated innovative projects including:
- The installation of motion sensor operated lighting throughout six water treatment plants operated by Allwater.
- Creating an energy dashboard on the Allwater intranet to display energy usage, and to communicate information regarding energy saving operational tips and projects.
- Developing an energy savings calculator to aid procurement of power rated equipment for operations.
- Development of a water pump efficiency tool to monitor and highlight decreases in performance which may indicate the pump needs maintenance or replacement.
Key performance indicators
An important aspect of energy management under ISO 50001 is to monitor energy performance. This allows improvements in performance to be quantified, and for deviations in expected performance to be observed and rectified in a timely manner. Allwater tracks several Energy Key Performance Indicators (EnPIs) monthly, with trends reported to the relevant management and operational staff to bring focus to any deviation in performance. EnPIs include site wide energy efficiency metrics for wastewater and water treatment plants (i.e. kWh/ML).
More detailed metrics are used to monitor key areas in more depth. For example, utilisation of biogas is a significant factor in energy efficiency at wastewater treatment sites. Subsequent EnPIs include monitoring of biogas engine reliability (proportion of time available excluding planned maintenance) and start-up reliability (successful starts per total start attempts). Aeration power consumption (i.e. kWh/ML) is another focus area tracked for wastewater treatment. The EnPIs help the business define the areas of focus and the long-term trends enable understanding of the improvements done in each area, as seen on Figures 3 and 4. Significant improvements were made on the wastewater side over the last few years. A major focus for the business is now to understand, optimise and sub monitor as many water pumping stations as possible, to achieve a minimum of 1% energy usage reduction by 2020.
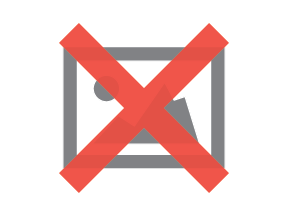
Note: power generated and consumed onsite is included within energy consumption for this metric.
Examples of key energy management initiatives
Reducing biogas flaring
Allwater produces approximately 58% of its overall wastewater treatment electricity requirements through the anaerobic process at three Wastewater Treatment Plants (WWTPs): Bolivar, Glenelg and Christies Beach. The methane generated during the process is converted into electrical power and used onsite. Any biogas that is not used for power generation has to be flared onsite as at present none of the WWTPs have extra biogas storage capacity. Management of the biogas is important to produce as much as possible as well as reduce biogas wastage through flaring.
Biogas power generation has reduced Allwater’s overall external electricity requirement by 20%. This fact highlighted the significance of any major plant failures affecting onsite power generation, resulting in the highest level of ‘criticality’ given to preventative maintenance programs. Table 2 shows the reduction in biogas flaring from 9% in 2014/15 down to 1% in 2017/18 at Bolivar since the Energy Management Program was implemented. This was achieved through optimisation of the control system and of the digester operation for optimum biogas generation.
Co-digestion implementation at Glenelg WWTP
The anaerobic digestion process at Glenelg WWTP produces biogas converted onsite by three combustion engines for electricity generation. Historically the digesters were only fed with primary sludge and thickened secondary sludge drawn from the wastewater treatment process, which produced enough biogas to provide approximately 55% of the power used onsite. Adding high strength trade waste to the anaerobic digester has two main advantages: (i) it can boost biogas production to produce more energy and (ii) it also avoids overloading the sewer and secondary treatment systems with trade waste.
Implementing co-digestion of different types of substrates, such as beer, wine, grease trap, dairy farms, etc. has enabled this site to increase its self-generation from 55% to up to 90%, as seen on Figure 5.
Intermittent mixing in anoxic zones
The goal of mixing in an anoxic zone is to keep the mixed liquor suspended and in contact with primary effluent and dissolved oxygen. As part of an energy efficiency review of several WWTPs, it was identified that the mixing of bioreactors was a priority area to improve. The mixing in the anoxic zones was operated 24/7, however, industry practice showed a trend towards allowing the operation of mixers in intermittent mode, with the setpoints determined by operators at each individual WWTP.
In order to achieve this, each mixer was assigned an option in SCADA for the operator to define the on and off period during normal operation. In tanks where two or more mixers were installed, the control system was changed to allow for the mixers to operate alternately. During operational trials it was noted that, on the whole, intermittent mixing was successful and the optimum on / off operation varied between seasons and between WWTPs. However, it was discovered that any anoxic zone containing online analytical equipment required mixing 24/7 to ensure continuous accurate measurements were relayed back to SCADA.
The intermittent mixing has been estimated to save at least 300 MWh/annum.
A solution to reduce energy consumption even further is the replacement of the existing mixers by equipment with motors utilising permanent-magnet technology. The measured energy savings between classic and permanent-magnet technologies is 10 to 15%. Allwater is progressively replacing mixers with permanent-magnet technology as an ongoing maintenance program.
Christies Beach WWTP flow split optimisation and advanced aeration
The Christies Beach (CB) WWTP completed a major upgrade in 2012/13 with a 50% increase in plant capacity for projected growth and load in the catchment area over the next 25 years. The basis of CBWWTP design was to provide capacity to treat an annual average flow (AAF) of 45 ML/d. The existing A and B plants take half of this flow (22.5 ML/d) with a new membrane bioreactor (MBR) C plant constructed to take the balance (22.5 ML/d). The upgrade was also to ensure the required effluent discharge target of 100 tonnes / year of total nitrogen was met. An overview of the site is shown in Figure 6.
The MBR plant is an energy intensive process due to the aeration requirements of the membrane filtration process and increased mixed liquor concentration within the bioreactors; however, the process ensures high quality effluent for both suspended solids and nitrogen so our Environment Protection Authority discharge obligations can be achieved. The final completed plant saw electricity power usage double, however, sewage flow to the plant was only 70% of design. A detailed investigation was undertaken to develop an operating strategy that considered the ideal flow distribution through plants A, B and C to achieve the target TN discharge load and minimise energy consumption at CBWWTP.
The resulting study showed that during the summer months, when effluent reuse was highest and discharge to sea was minimal, the design flow to A and B plant was maximised and one of C plant’s bioreactors was taken offline. This strategy resulted in an effluent with higher nutrients, but these were of benefit to the local irrigators who receive the treated effluent. During the winter months when effluent reuse was minimal, the reverse operation could be instigated with flows to C plant maximised and either A or B plant taken offline. This flexibility in operating strategy delivers an estimated energy saving of 700 MWh/annum.
Allwater is now undertaking a trial of advanced aeration control at CBWWTP. This is a predictive aeration control based on ammonia load into the biological treatment stage, and feedback correction on actual treatment performance. Safeguards are in place to maintain dissolved oxygen within an acceptable range prior to effluent clarification so energy consumption can be reduced without compromising nitrogen removal. Indications to date suggest a further 15% saving in aeration power costs and savings in carbon dosing of around 30%.
Other process initiatives
A number of other process initiatives have been implemented across the business including:
- Control system improvements to optimise energy usage and increase operation flexibility;
- Demand management with the SA Water OCC (Operations Control Center) notifying Allwater operations of forecast events;
- Networks demand management where pump start/stop level setpoints are entered as a function of time and manual adjustment of level start/stop setpoints for forecast high price events.
Energy recovery and way forward
As mentioned above, a major focus for the business is now to understand, optimise and sub-monitor as many water pumping stations as possible, to achieve a minimum of 1% energy usage reduction by 2020, with the new target defined as part of the ISO 50001 energy review.
To achieve this, Allwater is also investigating energy recovery processes such as mini-hydros. A hydro electric turbine (a Francis-style turbine with a rated maximum output of 1.16MW at 1,525 L/s) was installed to operate as the primary pressure reduction device supplying water from the main water treatment plant in Adelaide directly to the end user within the western Adelaide transfer system. Targeting a downstream pressure setpoint, the turbine modulates output flow rate to meet the network requirements. Normally wasted energy from the pressure reduction process is recovered through the turbine and exported to the grid. Figure 7 shows that ongoing power recovery has occurred thanks to the turbine.
This initiative also contributes to the SA Water target which is to achieve zero net electricity cost by 2020. SA Water are investing in renewable technologies such as solar panels and Allwater are aiming to use even less power onsite and move towards self-sufficiency on two of the biggest WWTPs with reduced reliance on the electricity grid.
Conclusion
Allwater has established an ISO 50001 Energy Management Program to drive operational energy efficiency across its operations. This has resulted in greater access to energy usage information across Allwater and associated reporting systems have been developed to identify usage trends. From this improved understanding of energy usage, opportunities for energy efficiency have been identified and implemented and
led to:
- 9% total energy consumption reduction from 2014 to 2018;
- 53% increase in biogas produced and 85% reduction in biogas flared from 2014 to 2018;
- 20% reduction of electricity imported due to improved biogas generation;
- Control systems improved to optimise energy usage and increase operation flexibility;
- Implementation of smart controls.
The Energy Management Program has been a success and Allwater, SA Water, and its customers will benefit from these energy reductions identified and implemented, with potential for further savings in the coming years as more energy efficient projects and initiatives are completed.
About the authors
Jennifer Dreyfus | Jennifer is a process optimisation engineer in wastewater and energy at Allwater. She has been working in the water industry for the last 10 years. Her focus is on implementing innovative processes to improve operations, environmental impact and energy consumption of wastewater treatments across all sites.
Greg Oates | Greg is a process optimisation engineer for Allwater, working on water treatment and energy in Adelaide. He has 10 years of experience spanning operations and design in gas, energy and water.