Vibrations turbo charge green hydrogen production
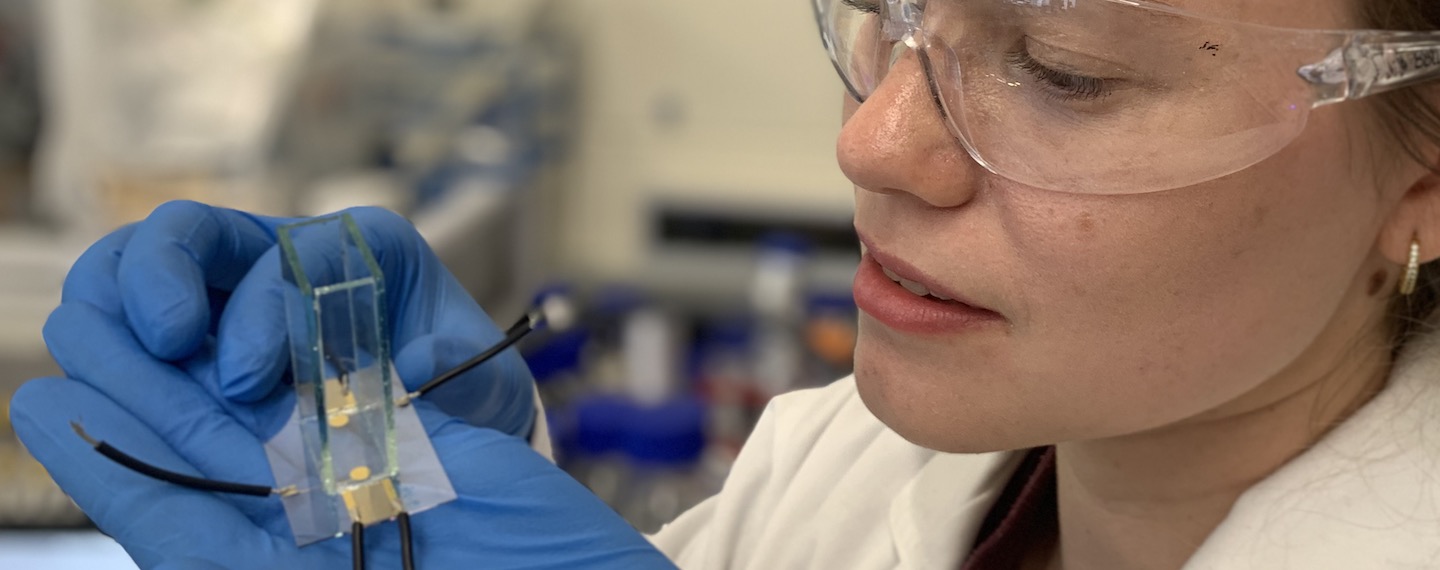
As the water community continues to strive towards net zero, more cost-effective and efficient green hydrogen is a development that many within the sector are keen to see progress. A recent study has delivered promising results using sound waves to improve the process.
Published in Advanced Energy Materials, the invention uses high-frequency vibrations to split water molecules by using electrolysis to release 14 times more hydrogen compared with standard techniques.
Electrolysis involves running electricity through water with two electrodes to split the molecules into oxygen and hydrogen gases, which appear as bubbles.
While green hydrogen is the most sustainable way to produce the resource – compared to blue hydrogen, which emits greenhouse gases into the atmosphere – it represents just a small fraction of hydrogen production globally due to the high energy required.
But RMIT Associate Professor Amgad Rezk said the research team’s innovation tackles big challenges for green hydrogen production, including the need to lower the cost of production and increase efficiency.
“One of the main challenges of electrolysis is the high cost of electrode materials used, such as platinum or iridium,” he said.
“With sound waves making it much easier to extract hydrogen from water, it eliminates the need to use corrosive electrolytes and expensive electrodes such as platinum or iridium.
“As water is not a corrosive electrolyte, we can use much cheaper electrode materials such as silver.”
Both the increased efficiency of production and the ability to use low-cost electrode materials, avoiding the use of highly corrosive electrolytes, are game changers for lowering the costs of producing green hydrogen, Rezk said.
Good vibrations
First author RMIT PhD candidate Yemima Ehrnst said the sound waves increase the efficiency of the process by preventing a build-up of hydrogen and oxygen bubbles on the electrodes, greatly improving conductivity and stability.
“Electrode materials used in electrolysis suffer from hydrogen and oxygen gas build-up, forming a gas layer that minimises the electrodes’ activity and significantly reduces its performance,” she said.
Rezk said hydrogen ions combine and turn into hydrogen gas bubbles on the electrode surface, causing “gas build-up”, with the gas bubbles sticking to the electrode and forming a non-conductive blanket of gas, thereby limiting more hydrogen ions from forming on the electrode.
As part of their experiments, the team measured the amount of hydrogen produced through electrolysis with and without sound waves from the electrical output.
“With our acoustic waves, we disturb the bubble growth process, and so instead of the bubbles growing to a large size – half a millimeter – the acoustic waves assist in lifting them off the surface when they are the size of 50 micrometers, less than human hair,” Rezk said.
RMIT Professor Leslie Yeo said the team’s breakthrough also offers promising results when it comes to saving energy.
“Our ability to suppress bubble build-up on the electrodes and rapidly remove them through high-frequency vibrations represents a major advance for electrode conductivity and stability,” Yeo said,
“With our method, we can potentially improve the conversion efficiency leading to a net-positive energy saving of 27%.”
Rezk said this result is a significant improvement in terms of making green hydrogen production more energy efficient.
“Electrolysis is based on the electrical energy input, compared to the hydrogen output. Electrolysis efficiency is roughly 40 to 60%, due to the high resistance of the electrode-electrolyte cell and bubble build-up,” he said.
“Our technology provides an enhancement in the hydrogen output, for a given electrical input, and when the acoustic energy is accounted for, we still provide a net positive energy savings of 27%.”
Next steps
While the innovation is promising, the team needs to overcome challenges involving integrating the sound-wave innovation with existing electrolysers to scale up the work.
"We are keen to collaborate with industry partners to boost and complement their existing electrolyser technology and integrate into existing processes and systems," Yeo said.
Rezk said the research team is currently discussing next steps with companies that work in the electrolysis and electrolysers field for green hydrogen production.
“Our intent is to complement current electrolysers with our acoustic technology to boost the overall performance,” he said.
“The main challenges now are the research and development side of things, and the engineering work required to integrate our device into well-established electrolysers.
“The risk in testing our approach in a high throughput setting is whether the acoustics will be as effective, and the size limitations of our chip-scale device, although our chip can be mass produced at a low cost.”
Image credit: RMIT