Sand products to support filtration processes
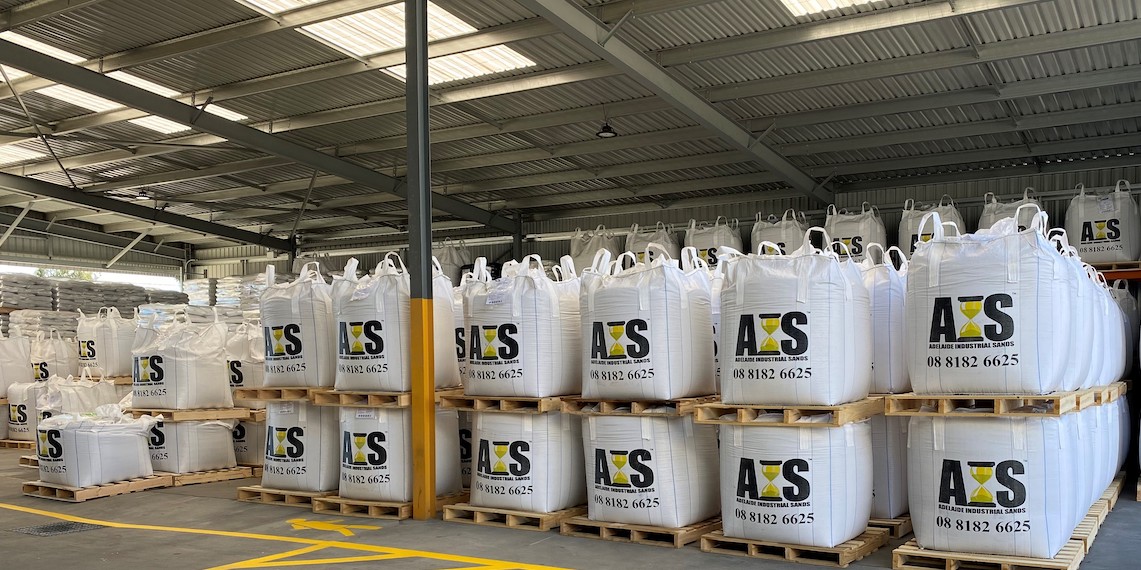
While most water treatment engineers will be aware that sand is used to help in the filtration process, the work that goes into ensuring the sand and gravel utilised requires more technical accuracy than might first meet the eye.
Adelaide Industrial Sands (AIS) have recently joined as a member of the Australian Water Association, with the company supplying many water utilities around Australia with customised sand products to support filtration processes.
AIS General Manager Joseph Tassone said the company has recently expanded its processing capabilities to meet the detailed specification requirements of varying water service providers.
“Sand has been used for filtration for a long time, as a means of cleaning water and catching dirt and debris. And, essentially, that's what our filter sand is there to do, to help water utilities with their treatment process,” he said.
“One reason why we joined the AWA is to get more involved in the technical side of this process so that we can better understand our client’s particular specifications. Our sand is high in silica, which makes it particularly useful for industrial water treatment processes.
“We are a relatively young company – we've been around for about 10 years – but we are finding our feet in the water sector. While we started with pool filter sands, it’s wonderful to see how well our products are now doing in the water sector more broadly.”
Tassone said that sand and gravel size are critical for large scale water treatment processes, and a big part of AIS’s work is ensuring that their product meets the tight specifications required for different treatment plants.
“We've found our inroads into some of these large-scale water treatment projects because we’ve been willing to customise our sand for different applications. We receive the washed sand from our sister company Clinton Sands, then bring it down to our plant where we process it further into those tight specifications,” he said.
“We work our raw feed through a fluid bed dryer, which is a new type of drying technology that is very energy efficient. The sand then gets put through our screening plant, which has different sized stainless steel mesh, or screens. Changing the screens enables us to ensure sands meet very particular specifications.”
Meeting specifications
AIS’s processing screens have different aperture sizes, which allows the plant to process the sand into different sizes, depending on what is required on application in filtering.
Once the sand has been processed into different sizes, Tassone said the work then involves a detailed quality control process, set to ensure that every tonne of sand supplied to the customer meets specification.
“We've learned that our water sector clients need to have confirmation that our sand meets their specifications prior to delivery,” he said.
“In order to ensure this, we test the very first bag we produce in our own internal lab. This helps us ensure we’ve got the formula right before we proceed. We then continue on and take samples at every four or five bags.
“These samples are then further tested within the lab, verified and approved. These results are then sent off to our client before dispatch.”
While AIS has met a few challenges after entering the water sector, Tassone said the company has been learning quickly and haven’t met a hiccup they can’t handle.
“There have been a few issues with logistics that we have had to work through. Some of our water sector clients have treatment plants located in areas that are hard to access, and so organising transport of our product has been a hurdle in some instances,” he said.
“But, so far, we haven’t met a challenge we haven’t been able to overcome. We are doing more and more work within the water sector and we have well and truly gotten into the swing of things now.
“We’re looking forward to continuing this work with the sector. It’s great to know that our products are helping achieve great results for our clients.”