How to refurbish a WWTP in just six weeks – without taking it offline
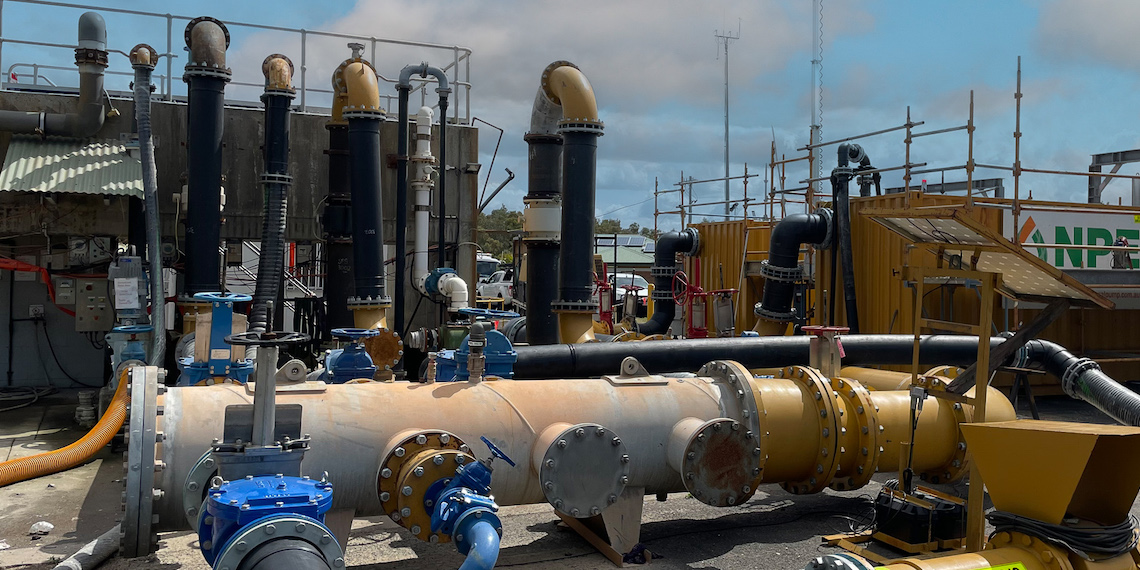
One single wastewater treatment plant serves all of Byron Shire Council in northern New South Wales, which means that any maintenance operations that need to be carried out require careful planning.
When pumping and power generation solutions provider National Pump and Energy (NPE) was called in to ensure the Byron Bay sewage treatment plant’s ageing infrastructure could remain operational while undergoing refurbishment, the NPE engineers were faced with a number of challenges.
In particular, the plant’s entire inlet works would have to come offline while the strip-out and recoating was undertaken.
Delegate Lounge sponsor of Ozwater’23, NPE had to ensure its operations could continue uninterrupted across during the full-length of the maintenance period. And it all had to be done in a tight timeframe of just six weeks.
“They needed to have the ability to provide a screening solution and bypass while they took the inlet works offline – and a solution that enabled their downstream treatment process at the plant to continue as normal without impact,” said NPE Eastern Region Business Manager Tim Alexander.
“So that was our scope, to design a system that would provide a temporary bypass of that inlet works to enable them to complete their repair work without any other impact of disruption of the plant.”
There were other considerations, too, including the Splendour in the Grass music festival, which was due to take place during the maintenance period, drawing visitors from all over the nation to the Byron Bay area and substantially increasing the local flow rates into the treatment plant.
A busy – and wet – summer was also approaching.
“Once we provided some solutions and we went through a procurement process, we had a fairly tight window to deploy on site – and that coincided with what was a fairly wet and rainy summer,” Alexander said.
“So it was critical that we get this system operational and make sure that works were completed prior to the Christmas period. Obviously, timing and planning was absolutely key.”
Complex night works
During commissioning, the NPE plan sprang into operation at nine o’clock each night.
“The idea was to cut the plant over during the night shift. There are seven individual lines that fed the inlet works: four rising mains from the pump stations in the areas around Byron and three separate local plant pump lines,” Alexander said.
“We had to identify all the isolation points. We had to determine that there was adequate retention time in those pump stations upstream to allow adequate time for cut over each night. And we had to then forecast a program of works in terms of timeframes to cut that network over.”
It was also important, Alexander said, to pressure-test and leak-test the system’s pipe work to ensure that it would be fit for operation at each stage of the cut-over process, all while the network remained live upstream with the stations continuing to cycle as normal once the rising mains were cut over.
“We cut each one of those rising mains over and had all the pipework and fittings on site to do so, including critical spares for any unforeseen problems, and we did that one at a time,” he said.
“And once we'd torqued and tensioned everything, we then had to go back upstream to the pump station, remove the isolations that were put in place at that station and start the wet well pump down process to allow for normal cycle operations to be reinstated, which then involved another leak test to ensure that any of our temporary works back at the plant during the cut over were all sealed.
“We did that quite successfully on each of those rising mains as we cut them over, but it involved some tricky isolations. There were multiple pump stations feeding common rising mains, so we had to ensure that the isolations were all confirmed, effective and safe prior to NPE disconnecting all the pipe work and re-joining it to our temporary works system.”
Boosting capacity
By the time the works were complete, NPE had processed and screened more than 250ML of wastewater through the system, with a maximum flow capacity of 340 litres per second. Alexander believes that crucial to the success of NPE’s system was ensuring that redundancy was built into it.
“Upsizing and having additional capacity meant that in the event that there was an unprecedented or prolonged increases in flow, we had capacity to cater for that,” he said.
“That included additional standby equipment, additional pipework, along with additional resources on call to cater for anything that might arise as part of the 24/7 monitoring and operation of the plant.
“Once we had cut over the rising mains from each of the pump stations upstream, NPE was 100%in control and responsible for the screening through our temporary and mobile inlet works we deployed to site downstream at the wastewater treatment plant.
However, Alexander said NPE had no control of the individual pump station operations: “This meant that we needed to have the ability within our system to cater for all stations running concurrently for prolonged periods of time during increased flow events like storms or heavy rain periods”.
“We didn't have the luxury to quickly cut the rising mains back over nor was there this ability, as the permanent inlet works had been decommissioned for refurbishment. This meant confidence in NPE’s temporary solution to perform with built-in redundancy and additional capacity as needed was critical.
“Once we went live, we were providing the entire screening process for that network incoming into the Byron Bay Wastewater Treatment Plant, we had to ensure that there was no risk of overflow or spill to the sensitive local environment.”
Despite these challenges, Alexander believes NPE’s success demonstrates that bespoke solutions are available for ageing infrastructure networks, and water authorities should explore their options.
“It often calls for an out-of-the-box idea, and that's how we build on these successful projects. We do so with engineering support behind us, and we make sure that we have redundancy built into the system,” he said.
“We've got a lot of experience in this space. We understand the critical, environmentally sensitive nature of this type of works, and the risks associated with wastewater spills.”
Interested in learning more about NPE’s work and capabilities? Visit them in the Exhibition Hall at Ozwater’23.