Practical monitoring and automated reporting on Health Based Targets (HBT)
By P Wootton, G Sharp, T Gray, O Taudou and D Hoefel.
First published as an Ozwater'18 Conference Paper.
Abstract
The release of the Manual for the Application of Health Based Treatment Targets (HBT Manual) and subsequent Good Practice Guide to the Operation of Drinking Water Supply Systems for the Management of Microbial Risk (Good Practice Guide) provided a good indication of the future direction for the Australian Drinking Water Guidelines (ADWG). It was identified that many of the performance criteria defined, could be measured using existing online data. To inform the process of ADWG development and progress plant performance towards future compliance, a body of work was undertaken to automate reporting against these new criteria that identified some practical issues and plant constraints in the process.
Introduction
The current major developments drafted for the ADWG are around the concept of Health Based Targets (HBT). The issue of the HBT Manual and subsequent Good Practice Guide, provided detailed information of how the HBT would work and what is covered. These targets are broad and cover a diverse range of topics, including:
- infrastructure configuration (e.g. the requirement for no interconnection between raw and treated water);
- workforce capability (e.g. plant operator experience and training); and
- plant performance based on sampling results and online monitoring.
To inform the process of ADWG development and progress plant performance towards future compliance, the plant performance targets based on online monitoring were given particular focus. This involved a survey of all targets to identify which could be measured using currently available online data, followed by the development of automated reports to monitor this performance.
Context
Allwater is a joint venture between Suez and Broadspectrum. Allwater has entered into an alliance contract with SA Water for the operation and maintenance of water, wastewater and recycled water systems in metropolitan Adelaide. For the context of HBT compliance with online data, the area of focus is the operation of six water treatment plants (WTP) that supply ADWG compliant water to metropolitan Adelaide and some adjacent country regions.
The six metropolitan plants (to be referred to as plants A through F for this report) are all conventional WTPs that use Alum as the primary coagulant, gravity sand filters for filtration and chlorine for disinfection. Five of the plants have large sedimentation tanks prior to filtration, with the sixth using dissolved air flotation (DAF) prior to filtration. The plants came on line and transitioned Adelaide from an unfiltered supply to a filtered water supply progressively, starting in the late 1970s and finishing in the early 1990s. Design capacities of the plants range from 50 ML/d to 850 ML/d, however, changes to required performance standards and capital upgrades over time have generally decreased capacities with current nominal capacities ranging between 45 ML/d and 450 ML/d.
Depending on the plant, pH correction is undertaken using quicklime, hydrated lime or caustic soda (or a combination). Only one plant (Plant A) uses acid to control coagulation pH to an optimal level. All plants use polymer as a coagulant / filtration aid, and fluoride dosing is also common to all plants.
All six WTPs are automated using Programmable Logic Controller (PLC) based control systems that are monitored and controlled via SCADA systems built on the iFix platform. This system allows operators to monitor and control the plant, to trend data, and to alarm failures on the plant. Paging of alarms is handled outside of the iFix system by separate software. Data collected by the iFix system is captured by iFix historian servers and retained for access through the iFix platform. For reporting external to the SCADA system (and for formal reporting), data is collected from the historian servers by SA Water’s Operational Data Store (ODS) system. This system provides database access tools more widely to the business, particularly for reporting. It also provides a single database for storing and reporting on data that may come from a variety of sources. For the work completed on HBT reporting access to the data was through a Microsoft Excel add-in (called Pi) that enables direct interrogation of the ODS database and allows reports to be built using Excel’s native functionality.
The ODS system and the Pi add-in are currently used for Allwater’s WTP performance reporting. This meant HBT reporting could be developed using these existing tools and knowledge as an extension of current practice.
Methodology
The process undertaken was simple but iterative. The initial step was to review the HBT targets as defined in the Good Practice Guide against the instrumentation that is present on the plants that are connected to the SCADA system. This identified a number of targets we could attempt to report against using existing available data.
Initial work was confined to a single WTP, with a draft report created against these targets. This required some assumptions to be made, which were then examined in detail at a workshop. The workshop identified a number of changes that were required or issues that needed to be addressed, with the report then re-drafted and re-workshopped to address the identified issues. This iterative process took a number of cycles to reach an end point.
The first plant to be tackled was Plant D and following completion of its report, the template was then able to be moved to other plants. Not all plants are configured identically, so further evaluation and development was required on a site-by-site basis to achieve consistent outcomes.
Data details
The ODS system records data from the SCADA system when there is a change in value, rather than at a consistent sample rate. The Pi tool then gives different methods of extracting this data depending on how it is required. The raw data can be extracted, but typically it is more useful to have Pi automatically interpolate between actual data points giving a result for any specific time that it is requested. Working in Excel for calculations, particular consideration was given to targets that require compliance for a percentage of time in the day or month. It was decided that whilst using the actual data points in ODS could be worked through, for Excel using a consistent sampling period made calculations and report set up much simpler. The consistent number of samples each day allowed formulae and sheets to be set up with a consistent number of data points to calculate or display. Using actual data points would require the ability to handle data sets that are not time aligned and as such would require interpolation of some sort to be done at times to enable calculation.
This decision then requires further decisions to be made about the data, specifically the time period and the method of interpolation used. In this case these were both decisions that had previously been made for existing reporting from ODS. Data points are taken each minute as an average interpolation of that minute period. This has proven to be a good compromise between data resolution and ease of data processing / handling. The method of interpolation has not shown to create major differences in data sets. When looking at a one minute interval on a large conventional water treatment plant there are very few parameters that change at high rates. Hence whether an average or a point interpolation is used over a one minute period, results are very similar. In some instances the average interpolation has anecdotally given more stable results than using an alternate interpolation method.
Processing details
With a view to the future HBT, reporting was set up to integrate into Allwater’s current data reporting process. This means checks and calculations are carried out at the same time and in the same way as the current system, ensuring readiness for full implementation of the HBT.
The process in place involves two stages of checking prior to monthly reports being completed. The first is a daily calculation and check. This is a process where a plant process technician will - on a daily basis - log into the system and the daily report will calculate performance against the targets for the single day in question. This allows any data issues to be detected and rectified in a timely manner. For targets that are monthly, the consistent data period of one minute allows rolling counts to be maintained, easily giving month-to-date performance and at the end of the month giving full month performance without having to calculate a whole month at a time. This method of daily calculation helps considerably in making data manipulation easier.
The second stage of checking is a weekly check by a plant supervisor, this stage does not complete any additional calculations but ensures an independent check of the data is made to double check for any anomalies in the data.
Specific targets
Continuous operation
The Good Practice Guide specifies that “Plant operation should be continuous where possible”. There are two measures listed to be assessed: monthly being an average percentage of daily operation, and an average number of plant starts per day. With the aim to be as close to 100 per cent operation and zero starts per day as possible.
These measures are simple to calculate using the plant raw water flow meter tag to indicate when the plant is in operation.
Results have been as expected, with very high percentages of daily operation and low numbers of starts, as the plants in question are generally run continuously. This measure has been found to give high level feedback very simply as to whether there have been operational problems on a plant. Figure 1 shows results from one of the plants. The plant faced specific raw water challenges through November and February, while in July through to September there were a number of capital upgrades taking place which required plant interruptions. The results clearly show a difference between these periods and a more normal period of operation such as seen between March and June.
Raw water flow management
To protect the filters on a conventional WTP, minimising the rate of change of flow is good practice. This has been defined in the HBT to be 95 per cent of flow changes being less than 3 per cent per minute and 100 per cent of flow changes occurring at less than 5 per cent per minute on the raw water.
These criteria are interesting to try and calculate as a threshold needs to be chosen to count a flow change. Five of the six plants examined are either fed by variable speed pumps or variable control valves. A number of the plants have control systems to track demand flows and hence can be varying the raw water flow continuously but slowly. The sixth plant has fixed speed pumps so each flow change comes as a step change for example from 40 ML/d to 70 ML/d.
As an example, of one the findings during this project on 3 of July 2017 the data for Plant D shows that there were 441 minutes when the flow changed by more than 3 per cent and two minutes by more than 5 per cent. This is a comparison of the raw water flow minute by minute. The plant ran for 24 hours and at a constant flow (i.e. the same pump ran at full speed for the whole 24 hour period). Figure 2 reports the trend direct from SCADA and shows the noise on the trend to be considerable, typically varying by 1 – 2 ML/d each minute. At a flow of 40 ML/d a 1 ML/d change in a minute is 2.5 per cent hence the large number of apparent flow changes greater than 3 per cent for the day. On a fixed flow plant like this, filtering could be put in place (either on instrument, in control system or in the report) to filter this noise.
Plant A, a variable flow plant, was examined in the same way, with the plant running for 24 hours continuously on 19 July 2017. The data shows 370 minutes where flow changed by greater than 3 per cent and 29 minutes by greater than 5 per cent. Figure 3 shows the SCADA trend which again shows significant noise. Examining the ramp rates employed (ramping the plant up and down) the maximum rate of change is approximately 1.2 per cent per minute which is well within the target, yet the noise caused failure of the target significantly for the day.
In both cases examined, filtering could detect significant deviations from the target but to overcome the magnitude of noise present, filtering is required such that a flow change of 3 per cent per minute would need to be sustained for greater than 8 – 10 minutes to be picked up above the noise level. This can be achieved, but will not pick up short duration issues unless they are of a much greater magnitude.
A more significant issue identified during the development of these reports is that by restricting and examining the rate of raw water flow change it doesn’t sufficiently protect the filters from flow shocks. The plants being examined have between six and 16 filters and at low flows many of the plants will operate on only two filters. Incidence of poor filter performance were identified while the HBT flow change targets were being met (if data filtering was used). These were primarily when a filter came offline for backwash and significantly increased the load on other online filters. While these flow changes could not be measured as there are no flowmeters in place it would be possible to increase the flow on a filter by 100 per cent in only a few minutes as one filter inlet valve closes for backwash prior to another filter coming online. This issue is discussed further, relative to the target for flow management during backwash.
It is considered that the HBT target could be revised to better target individual filter performance. This would have two primary benefits: more directly addressing the health risk, and for larger plants with multiple filters it increases flexibility as plant ramp rates could be increased beyond the target rates if filters were controlled suitably to avoid fast rises in filtration rate.
Clarification
There are only four measures for clarification specified, and only one of these can be checked using online monitoring data. This is the requirement to have clarified water turbidity of < 2 NTU for 95 per cent of the month and < 5 NTU for 100 per cent of the month (settling clarifier).
Using the decisions already made about data processing this was simple to calculate using data with a one minute sample rate and the formulae provided in the Good Practice Guide. The difficulty encountered was trying to automate the report to recognise sedimentation tanks being taken on and offline. The ability to achieve this came down to what assets were available on each plant with most plants having no SCADA indication/signal as to whether a sedimentation tank was online or offline. To overcome this as part of the daily operator checks, a tag is stored within the ODS system flagging whether a sedimentation tank is on or off line. As tank status is not changed frequently this has proven to be a satisfactory way of achieving the reporting required.
Upon examining the results of this target at different plants there were no surprises revealed with better settling performance generally corresponding to better filter performance. Compliance has also been found to be relatively good with only minor failures found.
Residual management
Two targets are given for residual management both of which were able to be reported on with existing data. Not all of the plants examined have residual return streams but those that do have the return rate controlled to a percentage of raw water flow. However, the return systems are limited by the infrastructure on site. Development of the reporting was relatively straight forward as tags are already stored for plant operating status, and flow data is available for recycle and raw water flows.
The targets particularly refer to limiting the recycle stream flow to less than 5 per cent of the plant inflow and to maximising the time the recycle stream operates. Together these targets should improve the consistency of the plant feed water and minimise the amount of recycle being treated at any given time. Examining results, however, clearly demonstrated the limitations of the infrastructure on site and the way it is controlled. For example on Plant C there was typically no compliance with the less than 5 per cent recycle flow criteria yet the time that the recycle stream was operating was only between 15 and 20 per cent of the plant operation time. These targets clearly indicate that improvements can be made on this situation. In this case the limitation is the recycle pump itself having a minimum flow ability that is typically above 5 per cent of the plant inflow requiring further investigation to efficiently address this issue.
Media filtration
The Good Practice Guide focusses heavily on filtration performance with a number of issues highlighted. Most are not able to be directly measured with online data, with the exception of some of the most critical criteria on individual filter turbidity aimed at pathogen removal. Reporting was put in place for turbidity reporting to both the 4 log and the 3.5 log Cryptosporidium removal criteria. For this report the 4 log criteria of individual filter turbidity being below or equal to 0.15 NTU for 95 per cent of the month and not greater than 0.3 NTU for greater than or equal to 15 minutes will be examined. It was identified that a subsequent requirement of the Good Practice Guide to have 95 per cent of ripening periods be less than 0.3 NTU within 15 minutes would be covered by the initial target and only would become an issue if the initial target was failed.
Set up of the reports did not pose any issues as all of the data required was available, including valve status to indicate what status a filter is in. The detection of ripening spikes for the secondary target was examined but an arbitrary decision had to be made as to how close to a filter start-up a spike needed to be, to be a ripening spike. The decision was made not to report on these criteria as the overall criteria captured the occurrence.
Results against individual filter turbidity targets have been improved since working towards the targets began. Performance is now excellent against these targets with all metropolitan Adelaide WTPs complying consistently with the 4 log criteria. One of the key operational changes made to achieve the criteria is also the cause of identifying an issue with the target. Operation of the plants is now such that the number of filters in operation is dictated by how many filters are required to maintain a set filtration rate. Underloading filters historically affected their performance, limiting the ability to achieve the 4 log criteria. However, running variable numbers of filters can mean that during low flow periods not all filters run very often. It has been found that filters can fail the 4 log criteria because they started running on the evening of the last day of the month, had a ripening spike and then the month changed. The filter then goes on to run at low turbidity for a number of days fully achieving the intent of the target but not the detail of the target. This is a simple issue that is easy to understand but that should be understood by anyone checking compliance with these targets (note this issue could equally apply to any similar monthly type targets).
Flow management during backwash
The Good Practice Guide recognises that raw water flow control is not the only way that flow changes can impact on filtration rate and filter performance. As identified earlier, poor filter performance due to flow changes on filters can happen independently of raw water flow changes and particularly when backwashes are being undertaken. Hence the criteria is given to limit any increase in flow to filters remaining on line during backwash to < 20 per cent. The difficulty with this criteria is that we cannot measure it directly as there are no outlet flowmeters on each individual filter. In place of actual flow measurements, calculations were trialled based on the control system filtration rate calculation. Even though this is theoretical based on raw water flow and the number of filters online it was initially considered it may give reasonable results. Through development, however, it was found quite quickly that the use of a calculated tag led to theoretical results that could easily be proven not to be relevant even if actual results couldn’t be determined.
Figure 4 shows a trend of calculated filtration rate through two separate backwashes indicating essentially no change in filtration rate. Figure 5 gives a more detailed view of the first backwash shown in Figure 4. This trend shows when Filter 4 comes offline for backwash (the inlet valve closes) and the impact it has on the outlet valves of Filter 3 (online at the time) and Filter 5 (coming online to replace Filter 4). We can see the timing of the changeover led to the calculated filtration rate remaining steady, however, the outlet valve on Filter 3 increased in opening from 57 per cent to 69 per cent before coming back down as Filter 5 slowly came online. This change was also typical of the other filters online at the time. This may not have led to a flow change of greater than 20 per cent - and by the end of the backwash it hadn’t - but in other situations with fewer filters online, it could easily be shown to increase flow by more than 20 per cent for a short period.
The conclusion drawn from this examination is that whilst a better approximation of flows could be reported for this target (for example using the valve per cent opening, filter level and head loss to calculate a flow through the butterfly valve) the achievement of the target depends on control system programming. Hence effort is now being transferred to the control system with a view to compliance with this target and improving the smoothness of filter transitions.
Chlorination
The HBTs ask for chlorine Ct targets to be achieved for adequate disinfection either using data derived from tracer studies or using standard baffle factors. During this project three methods were trialled for calculation of Ct:
- Online Ct trending on SCADA derived from a full fluoride tracer study enabling real time Ct monitoring to be implemented.
- A conservative daily calculation based on the minimum tank level of the day, the maximum flow of the day and a poor baffling factor.
- Minute interval calculations using actual tank level, actual demand flow and a conservative baffle factor.
The calculations are relatively simple and in practice the results were all satisfactory after cleaning up some of the data. Method 1 provided the most accurate results however required a separate project to undertake the tracer study and implement the calculations into SCADA. Method 2 was trialled due to the simplicity of implementation but was found to give unrealistically low results some of the time although generally still compliant. Method 3 was not difficult to implement and provides a realistic estimate of actual Ct.
For this study all plants have a flow meter and a chlorine analyser on the outlet of the storage tank.
Conclusion
The process of implementing reporting against the HBTs has been an informative one. Each target has seen learnings of some sort that may help plant operation or may show a limitation in the target itself. Overall the HBTs provide incentive to improve operation and provide more consistent higher quality water. There are however some limitations that were discovered enabling feedback to be provided into the ADWG development process. These were primarily around measurement of raw water flow changes.
Other useful issues were found on filter control that should enable improvements that will reduce the shock that filters are subject to during normal operation.
By developing the reporting, the operation of the Adelaide metropolitan WTPs has been well informed about the new targets and positioned well for future compliance.
Ozwater is the Australian Water Association's annual international water conference and exhibition which takes place in alternating cities each May. To find out more, visit the Ozwater website.
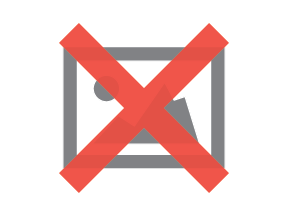
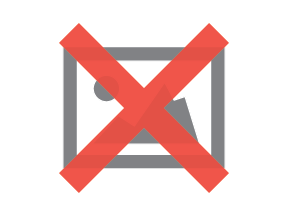
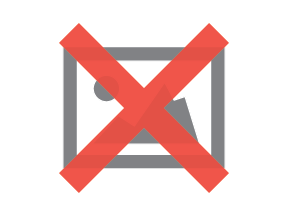
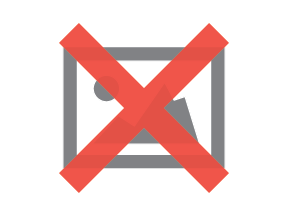
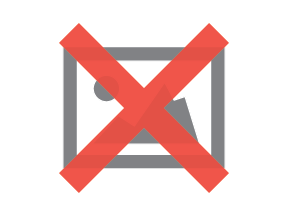