Choosing the right blower technology for low pressure applications
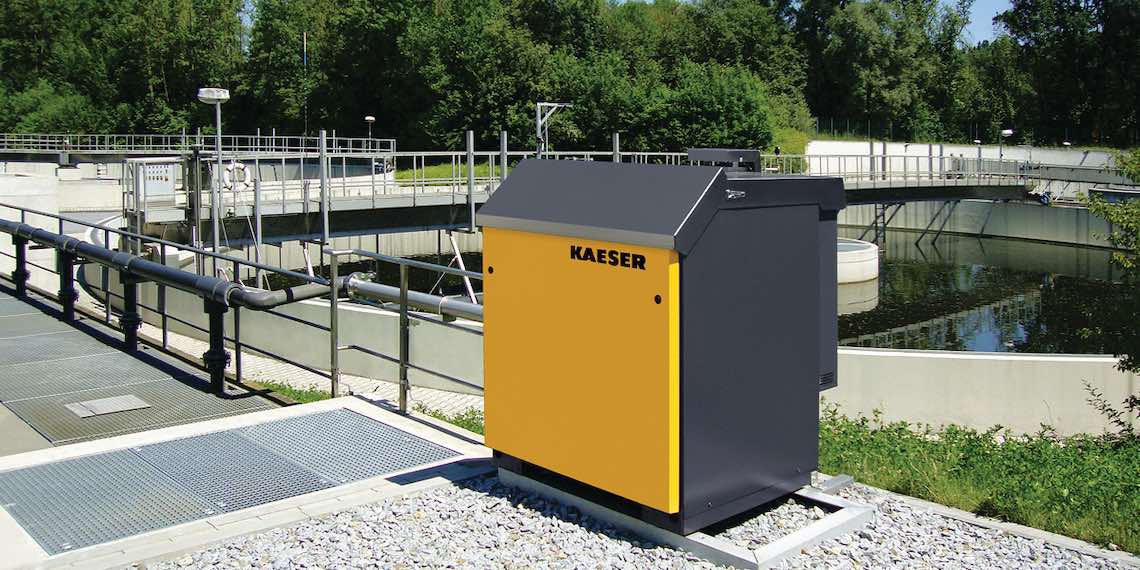
The different types of technology available for generating compressed air are many and varied: rotary lobe blowers, rotary screw blowers, turbo blowers, and many more.
With a wealth of options on offer, operators looking to purchase reliable and long-lasting equipment for applications such as wastewater treatment would be well advised to carefully consider the matter from an engineering perspective before making a decision.
Getting to grips with the technical differences
Companies operating in the fields of water treatment, fermentation and flotation have a broad spectrum of blowers from which to choose. Not only are there a wealth of different technologies and machine types available, but different terms are sometimes used to refer to the exact same machine, which can make selecting the right one a confusing business.
The most common types of machine for these applications are rotary lobe blowers, rotary screw blowers and turbo blowers, which generate differential pressures between 0.4 and 1.0 bar and flow rates up to 250 m³ per minute.
When it comes to generating compressed air, two different types of technology are available: positive displacement compressors and dynamic compressors. Rotary lobe and rotary screw blowers belong to the family of twin-shaft positive displacement compressors. Rotary lobe blowers are also sometimes referred to by the somewhat outdated terms of “rotary blowers” or “Roots-type blowers”.
The term “rotary screw blower” is now customarily applied to a single-stage, oil-free compression rotary screw compressor configured for low pressure operation. A look at the geometry of their respective rotors highlights the significant differences between the two types mentioned above.
Viewed from their cross-section, the male and female rotors on a rotary lobe blower appear virtually identical. Both feature three lobes and run longitudinally in a straight line. The volume of air between cylinder and rotor lobes remains constant as the rotors turn and throughout the compression process.
In the field of thermodynamics, this is known as “isochoric compression”. Pressure builds up in the process lines because the air molecules are constantly pushing against the prevailing resistance generated by the blower.
Robust and inexpensive to maintain, rotary lobe machines are recommended where differential pressures between 0.2 and 0.5 bar are required and, when operating at variable speeds, they can easily attain a control range of 1:3.
When combined with an integrated frequency converter, they achieve an isentropic efficiency of between 45 and 60 percent. Depending on the size of the machine, speeds of 2000 to 6000 rpm are common in the rotor shaft.
Download the Whitepaper to read on!
Download now: https://bit.ly/3MBapyt